Rub and scuff testing for your labels
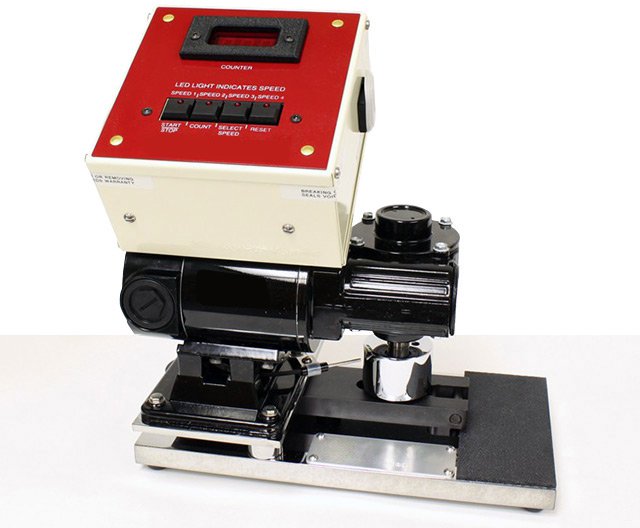
One of the most overlooked testing procedures for wine, spirits and beverage bottle labels is the rub and scuff test. It’s a simple test, but when utilized properly it can eliminate nearly all abrasion issues that may occur during transit and consumer use of your labeled bottles. The rub and scuff test takes place before, during and after the actual production of your labels.
The following procedure outlines the equipment, materials and steps involved in performing an accurate and repeatable rub test:
- A rub testing machine is required. If your printer is producing beverage bottle labels they should have one.
- When bottles are prepared for transport, the case boxes have cardboard inserts in them to keep the bottles steady and firm in the case. Your actual inserts are the best tool for your printer to use when performing this test.
- Your label printer will need a few printed and varnished production labels.
The rub and scuff test involves a standard two-pound or four-pound weighted block, with your packaging insert affixed to its base. This weighted insert is then dragged back and forth in an arc across the face of your label at its weakest point. With an embossed and foil-stamped label, for example, those areas would be considered the highest point that would show wear before the other parts of the label.
The purpose of the rub and scuff test is to simulate the pressure, rub, and vibration that takes place during transit of the packaged bottles. Our goal is to identify potential weaknesses and compensate for them before your labeled products are in the hands of your customers. In most cases, the minimum number of rubs required for a passed test is 2,000 rubs, with 5,000 rubs being preferred. The rub tester includes a digital counter, variable speeds, and a programable stopping point, making the final test results reproducible.

Utilizing a printer that performs consistent and repeatable rub and scuff testing each and every time is critical in maintaining the integrity of your label quality. Failure to perform adequate material testing and rub testing can compromise your labeled products and your brand.
It’s interesting to note that we have found when labels pass 2,000 rubs during the test, they can withstand travel of approximately 2,000 miles when properly packaged and boxed. Having said that, labels that travel further will typically require additional protection, such as extra varnish coats, to protect the labels from eventual damage.
Find the best solution that makes the most sense for your brand.
Tags: